石油焦煅烧过程中如何实现自动化控制
在石油焦煅烧过程中实现自动化控制,可以通过以下技术和方法来提高生产效率、降低能耗和提升产品质量:
1.自动化控制系统架构
石油焦煅烧的自动化控制系统通常包括三个层级:管理级(中央控制室)、控制级(PLC控制站)和现场级。
管理级:负责整个煅烧过程的管理和监控,提供人机交互界面,实现数据采集、处理、报警、报表打印等功能。
控制级:采用高性能PLC(如HOLLiAS LK系列),负责接收管理层的指令,对煅烧过程进行实时控制,并将现场状态反馈给管理层。
现场级:由检测仪表(如温度传感器、料位计)和执行设备(如电机、阀门)组成,负责采集现场数据并执行控制指令。
2.工艺控制策略
自动化控制系统对煅烧过程中的关键环节进行精确控制,包括原料破碎、上料、煅烧和排料。
原料破碎控制:通过自动化系统实现破碎设备的顺序启动和停止,确保原料粒度均匀,减少能耗。
上料控制:根据煅烧炉的料位和工艺要求,自动控制加料小车和输送皮带的运行,确保煅烧炉的连续进料。
煅烧过程控制:通过温度传感器和智能温控系统,实时监测煅烧炉内的温度,自动调整加热功率,确保煅烧温度的稳定。
排料控制:根据成品仓的料位和排料周期,自动控制排料阀的开启和关闭,实现煅烧后石油焦的连续排出。
3.智能温控系统
智能温控系统是自动化控制的核心部分,通过温度传感器实时监测煅烧炉内的温度,并根据预设的温度区间自动调节加热装置的功率。
温度监测:在煅烧炉的不同位置安装耐高温温度传感器,实时采集温度数据。
智能调控:系统通过比较实时温度与预设温度区间,自动调整风门和下火口的开启状态,确保煅烧温度的精确控制。
热能回收:结合烟气检测模组和烟气回流管道,实现烟气热能的再利用,降低能耗。
4.故障诊断与报警
自动化控制系统具备故障诊断功能,能够实时监测设备状态,及时发现并处理故障。
设备状态监测:通过传感器和PLC系统,实时监测设备的运行状态,如电机电流、阀门开度等。
故障报警:当检测到异常情况时,系统自动发出警报,并在中央控制室的监控界面上显示故障信息。
5.数据管理与报表功能
自动化控制系统能够对生产过程中的数据进行记录和分析,生成详细的生产报表。
历史数据记录:系统自动记录所有采集的数据,支持任意设定存取间隔和方式。
报表打印:根据用户定义的格式,系统可以定时、报警或随机打印生产报表,包括交接班记录、日报和月报。
通过上述自动化控制技术和策略,石油焦煅烧过程可以实现高效、节能和稳定运行,同时减少人工干预,提高生产效率和产品质量。
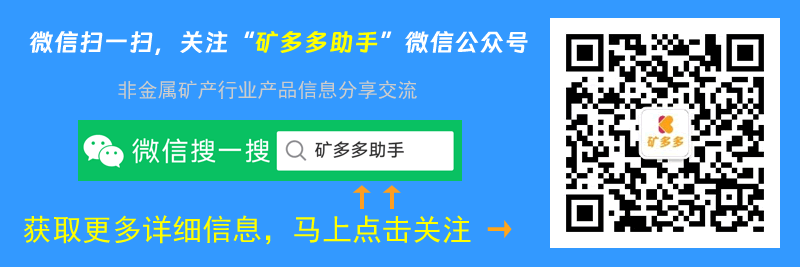
版权声明:本站所发布信息均整理自互联网具有公开性、共享性的信息,发布此信息旨在传播更多信息之目的,不代表本网站立场,转载请联系原作者并注明出处,如果侵犯了您的权益请与我们联系,我们将在24小时内更正、删除。